Light Gauge Steel Framing (LGSF) is a modern construction method that’s popular for its efficiency, sustainability, and versatility. LGSF is widely used in building homes, commercial spaces, and industrial structures because it’s durable and cost-effective. This blog will take you through the entire LGSF manufacturing process, from the design stage to the final construction, breaking down each step in simple terms.
Understanding Light Gauge Steel Framing (LGSF)
Before we get into the manufacturing process, it’s important to know what LGSF is. Light Gauge Steel Framing is a construction technique that uses thin, cold-formed steel sections to create a building’s framework. These steel sections are lighter and thinner than traditional steel, making them easier to work with while still being strong and durable. LGSF is perfect for projects where speed, accuracy, and sustainability are key. Delta-Green Structures LLP aims to provide the most durable LGSF services in all over India.
Design Phase: Laying the Foundation for LGSF Manufacturing
The design phase is the starting point of the LGSF process. It involves creating detailed architectural and structural designs with the help of specialized software. Here’s what happens during this phase:
- Site Analysis: The first step is to analyze the construction site. This includes checking the soil, climate, and other environmental factors that could affect the building.
- Architectural Design: Based on the site analysis, architects create the building’s layout and design. This design must meet the client’s needs and follow local building codes and regulations.
- 3D Modeling: Advanced software is used to create 3D models of the building, allowing designers to visualize the structure and make adjustments before moving on to manufacturing.
- Structural Design: Structural engineers then take the architectural design and develop a detailed plan for the building’s structure. This includes specifying the steel sections, connections, and other elements that will make up the framework.
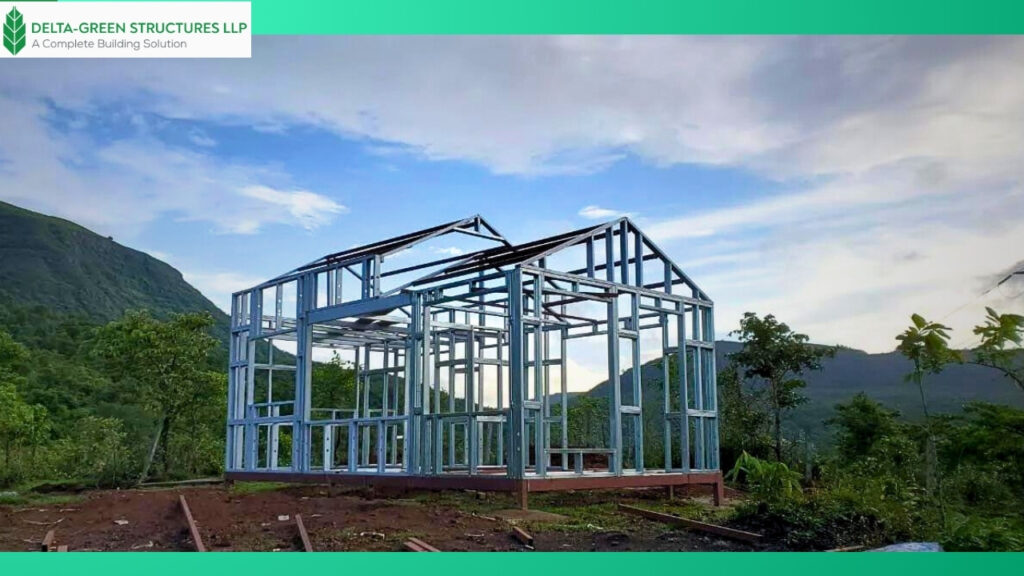
Fabrication: Turning Designs into Steel Components
Once the design is complete, the next step is fabrication. This is where the steel components are made according to the specifications in the design.
- Steel Selection: High-quality steel coils are chosen based on the required specifications. These coils are usually made from galvanized steel, which resists rust and ensures the structure lasts longer.
- Cold Forming Process: The steel coils are fed into roll-forming machines, where they are shaped into the needed sections. This process, called cold forming, is done at room temperature to ensure the final product is precise and strong.
- Cutting and Punching: The formed steel sections are then cut to the required lengths and punched with holes for connections and fasteners. This is a highly automated process to ensure accuracy and efficiency.
- Quality Control: Each steel component goes through strict quality checks to make sure it meets the design specifications. This includes testing for strength, accuracy, and resistance to rust.
Assembly: Building the Framework
After fabrication, the steel components are transported to the construction site, where assembly begins. This is where LGSF shows its advantages, as the lightweight components are easy to handle and assemble.
- Foundation Preparation: Before assembly starts, the building’s foundation must be prepared. This involves leveling the site and installing the necessary footings and baseplates to support the steel framework.
- Erecting the Steel Frame: The steel sections are then assembled on-site according to the Framing Drawing. The sections are bolted or screwed together to create the framework, guided by the 3D models created during the design phase.
- Integration of Services: Once the frame is up, other services like electrical wiring, plumbing, and HVAC systems can be installed. The open design of the steel frame makes it easy to add these systems without major changes.
Construction: Finishing the Building
The final step in the LGSF process is construction, where the building takes its final form.
- Cladding and Insulation: After the frame is complete, cladding materials like panels, or other external finishes are applied to the exterior. Insulation is also installed to ensure the building is energy-efficient and comfortable.
- Interior Finishing: Inside the building, walls, ceilings, and floors are finished according to the design. This includes installing drywall, flooring, and paint, as well as completing all electrical and plumbing work.
- Final Inspections: Once construction is done, the building goes through a series of inspections to make sure it meets all safety and quality standards. This includes checking the structural integrity, fire safety, and compliance with building codes.
Benefits of LGSF Construction
LGSF construction offers several benefits that make it a good choice for many projects:
- Speed: LGSF construction is faster than traditional methods because the components are prefabricated and require less on-site labor.
- Sustainability: Steel is a recyclable material, and the precision of LGSF manufacturing reduces waste, making it environmentally friendly.
- Durability: LGSF structures are resistant to fire, termites, and rot, ensuring a long lifespan with minimal maintenance.
- Flexibility: The lightweight nature of LGSF allows for flexibility in design and construction, making it suitable for various building types.
Conclusion
The process of LGSF manufacturing, from design to construction, is a streamlined and efficient method that offers many benefits for modern construction projects. By understanding each step, from the initial design to final construction, you can appreciate the precision and innovation that go into creating durable and sustainable buildings using Light Gauge Steel Framing. Whether you’re planning a residential, commercial, or industrial project, LGSF is a reliable and forward-thinking choice for your construction needs.